Manufacture
Furniture
Sales purchase management
Establishing a streamlined workflow for both procurement of production materials and the sale of furniture is crucial. This entails efficiently sourcing raw materials, ensuring quality control, and managing inventory for production to optimize operations, meet customer demands, and drive growth in the competitive furniture market.
Inventory Management
This involves maintaining optimal stock levels of raw materials and finished products to meet production demands and customer orders. Implementing robust inventory tracking systems enables real-time monitoring of stock movements, facilitating timely replenishment and minimizing stockouts or overstock situations
Module Customization for production
This entails tailoring existing software modules or developing new ones to align with specific production requirements and workflows. By customizing production modules, the company can streamline tasks such as scheduling, resource allocation, quality control, and reporting
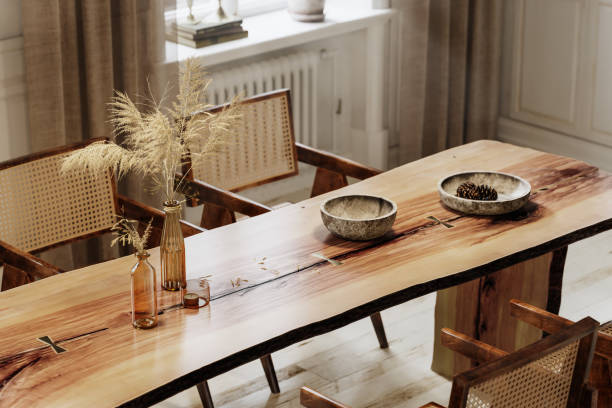
Furniture Company
One of our long-term clients, with whom we've partnered for 10 years, is a major player in the manufacturing industry, specializing in furniture. They're located in Central Java, Indonesia, and have been operating since 1998, boasting nearly 300 employees. Their capacity allows them to export 2-3 40-foot containers of furniture products daily.
Previously, they faced challenges in promptly meeting customer demands for specific materials or customized furniture, taking 7-10 days to estimate costs. However, through our collaboration, they can now estimate costs within a day, allowing them to focus on business needs more effectively.